Circular Economy in the Spare Part Management
This post gives an insight and overview regarding the main factors of an efficient circular spare part management within the food tech industry.
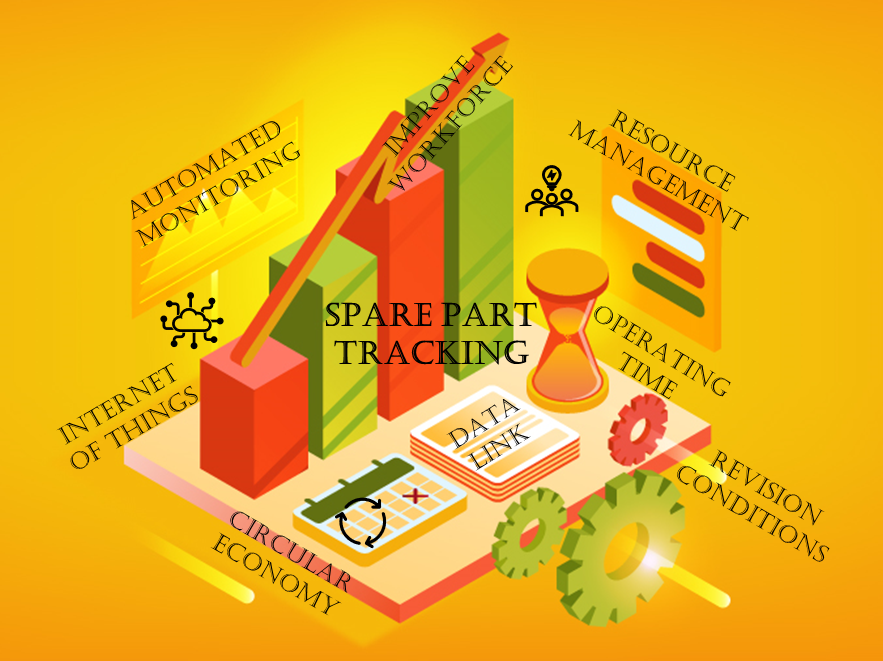
Topic
The vending machine business got more advanced with solutions that differ from the snack and beverage machines which are known since some decades now. The industry is facing challenges regarding the management of more expensive parts with the target of a minimal breakdown time of a machine and an easy way to change defective parts which are included in these newer food tech solutions.
Relevance
Spare parts became more modular and expensive, therefore the interest of their performance and lifetime increased. With the heightened thought of sustainability, the term of circular economy appeared. Comprehensible decisions during revisions in the workshop are required for an exchanged part from a machine or module. By answering the question of the main factors for an efficient circular spare part management and how these factors exert influence, this will help the industry to have an overview of these impacts. The results will show necessary roles and processes, improvements for the usage of recommended actions and it supports managerial decisions.
Results
The evaluation of the interviews led to the eight topics of important criteria, overlap of tracking and circularity, influence for the circular economy, sustainability, involved employees, limits and downsides, technologies, and further factors, where for every topic several factors have been identified. The factors have been compared to the literature part and the model of servitization has been enriched by the most mentioned factors of the interviewees. Additionally to the servitization model, there is the progression model with the main part of the organizational commitment and the four external influences of organizational readiness, customer pull, value network positioning, and technology push.
Implications for practitioners
- Existing options to use synergies need to be identified and implemented in the ongoing procedure.
- A business model needs to be established, to have a guideline through the whole process.
- The data which needs to be gathered must be defined and how it can be implemented into the existing company system needs to be evaluated.
- A monitoring needs to be created with defined KPIs that the procedure can be properly tracked and controlled.
- The company needs next to the own commitment and readiness to be aware of what the customers demand, how value can be generated for and with them, and which technologies will support for this value generating.
Methods
Existing literature already covers a lot of approaches for tracking and circular economy but occurring gaps regarding the spare part tracking have been identified through 11 semi-structured interviews with 19 practitioners from the food tech industry. The interviews have been split in company internal interviews of local employees, employees working within Europe for the company and further with external companies. The subsequent analysis was made with the transcripts of the interviews through coding them with the before mentioned eight main topics with corresponding subcodes. Comparisons afterwards with each other and discussing the results with the theoretical part indicated the current gaps.