Predictive Maintenance implementation to reduce downtime in intralogistics
This paper explores how companies implement predictive maintenance to reduce downtime in intralogistics, focusing on experts' insights on creating, implementing, and using this digital strategy for long-term success.
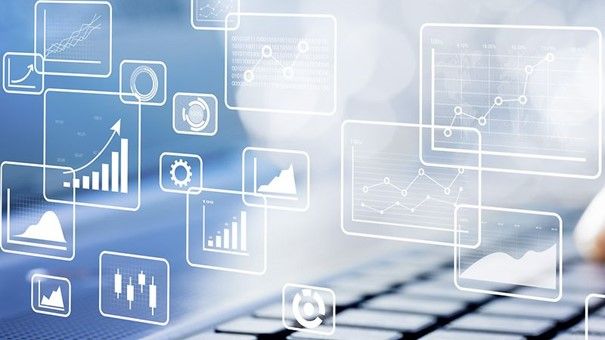
Unscheduled downtime in intralogistics can represent a massive disadvantage for companies. The implementation of a digital strategy using predictive maintenance is a decisive criterium for long-term success, as it ensures or even increases the availability of the plants where critical parts are monitored to mitigate the risk of failure. This paper examines how companies implemented predictive maintenance to reduce downtime in intralogistics. The focus of the research is to get insights from experts who create, implement, and use predictive maintenance in intralogistics.
Relevance
Predictive maintenance is a central theme in Data Science and can be used to reduce regular maintenance costs, increase service life, and improve sustainability. This study contributes to the awareness of how the implementation of a predictive method can generate long-term savings by reducing deficiencies and improving the plant. Further, the paper brings to light an important ethical point of view regarding the possibility of employees’ discharge because of the implementation of predictive maintenance.
Results
The results of the interviews showed that the benefits of implementing a predictive maintenance method include reducing regular maintenance costs, increasing a plant's service life, and generating long-term savings. Companies have taken a more structured approach, using risk analysis methods like FMEA and the experience of maintenance staff to identify critical parts of a plant. The paper also shows that no layoff was reported because of the implementation of a digital method but instead, a staff redistribution took place.
Implications for practitioners
Providing availability as a performance record can avoid contract penalties with the end customer.
Storage costs can be diminished since sensor devices will predict when exactly an element must be replaced, extending its use to the limit.
Shortage of skilled staff in today´s labor market must be considered in the decision of implementing predictive maintenance.
Maintenance activities can be scheduled based on the forecast turning the workplace more attractive since it is getting harder to find personnel willing to work on call.
Methods
The preferred method to achieve real expertise was semi-structured interviews with experts of the intralogistics branches to collect data based on the praxis approach. The data was processed in the following stages: transcription, anonymization, translation, and coding to allow an efficient delve into the obtained information. Qualitative content analysis followed a method described in the current literature. The verifiable program MAXQDA was used for coding. The evaluation of the interviews was divided into five important themes, respectively Preparation, Components and Elements, Implementation, Analysis, and Resources.